Wood grain patterns depend on cutting process
The way that wood is cut and the type of the wood itself determine how wood grains appear in sawn and cut wood.
One of the things that makes antique furniture so attractive is the beautiful wood grain seen in the better pieces. But how did the wood get that beautiful? Is it the wood or the stain or the finish or what? It could be any of those, but take a look at the wood itself first.
The second thing you notice about the wood, after taking stock of the color, is the wood grain itself. The grain could be seamless from end to end of a top surface, or it could be interrupted with stripes or designs or complications of the pattern itself, or even inclusions in the grain. With that, what determines how the grain pattern flows and whether it is straight or interrupted?
There are two primary factors that determine the wood grain pattern and direction in a piece of wood – the cutting process and the characteristics of the wood itself.
Wood cutting procedures
The most common way to cut a log into lumber is called flat cutting or plain sawing. This method continuously cuts boards from a log in sequential order, producing boards of varying width depending on the diameter of the log at each point and varying patterns in the grain. The most common pattern seen in plain sawn wood is the steeple, a series of interconnected long rounded points, all in the same direction. This is the most economical way to cut a log but there are other ways that produce wildly different results.
A popular, but less economical way is to quarter cut a log. The log is cut into four quarters and each separate piece is cut to lumber in a way that produces the maximum amount of wood grain pattern at right angles to the surface of the board. This produces the flakes or tiger eye seen in quarter sawn oak, either solid boards or veneer. Plain sawing the same oak log would produce a minute amount of flakes purely by accident in a small number of boards.
Veneer cutting
Cutting logs into veneer offers even more opportunities for influencing the grain pattern. Veneer can be cut from the intersection of major branch with the trunk or the intersection of two large branches. This is called a “crotch cut” and produces the flame or feather pattern commonly seen in antique mahogany and walnut pieces. Birch can also be successfully cut with a crotch cut. This cut is often mistakenly called “burl mahogany” or “burl walnut” by uninformed sellers or auctioneers. Crotch cutting produces a piece of veneer that is unstable and must be immediately attached to a secure surface. Crotch cut solid lumber is seldom seen because of the instability.
The single most commonly seen decorative veneer of the Depression era was stump-cut walnut. Stump cut is also known as butt cut veneer. This veneer was cut from the stump below the level of the ground where the roots begin to branch out from the stump. This creates a distorted wood grain pattern that is shown in the veneer.
The final way to cut veneer is the cheapest and thus the most common. A log is placed on a spindle and a thin sharp blade literally peels the wood off in a continuous strip of veneer hundreds of feet long that is so thin it must be backed with paper before it can be used.
Wood types influence pattern
So much for the way the grain can be influenced by the cutting process. The wood itself often has the final say in the appearance of the grain.
Curly maple
One the most popular variations is called “curly maple” or tiger maple” because of the wavy stripes seen in the wood. This was highly prized in Colonial American cabinetmakers and chair makers. The waves occur infrequently and randomly with no known cause in maple trees, and the amount of figure cannot be determined prior to actually cutting the tree and removing the bark.
Burl
Then there is burl. A burl is the highly confused and concentrated pattern found in some woods. The pattern consists of what appear to be small knots in a somewhat repeating pattern. Walnut burl and Carpathian elm burl from the mountains of France are most commonly used in American furniture making, although ash burl is seen occasionally as is American elm burl. There is no scientific evidence that clearly identifies the cause of a burl in a tree.
Bird's eye
Finally there is bird’s eye maple. This phenomenon appears as small, more-or-less round inclusions in the grain that are about the size and shape of a bird’s eye. (Thus the name.) But this inclusion does not have the small knots seen in burl. This pattern also appears to be infrequent and random and impossible to predetermine before cutting the tree.
There is much speculation about what causes these visually pleasing variations in the grain pattern. It could be genetics, trauma, fungus and soil conditions; they are all much discussed. But, a report from Auburn University says “the ultimate cause of figure in living trees is largely unknown.”
In short, there are lots of tricks and techniques that knowledgeable woodworkers can use to influence grain pattern in a piece of furniture. However, there are also certain instances where Mother Nature has her own design and we can only appreciate it.
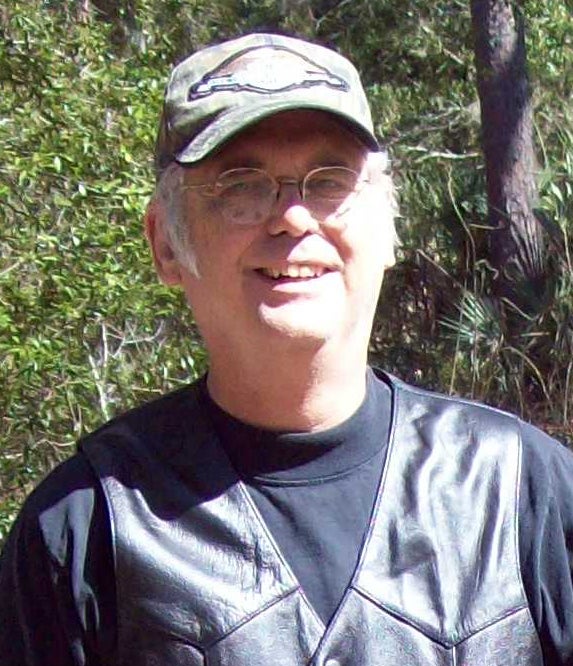
With more than 30 in the antique furniture business, Fred Taylor is a household name when it comes to the practical methods of identifying older and antique furniture: construction techniques; construction materials; and style.