Purpose of features aids in identifying wood chest
So often the naming conventions for items are about practicality. For example, in a response to a reader Furniture Detective Fred Taylor explains that a chest with a central compartment used to store bonnets and hats was referred to as a bonnet chest.
Q I would like to know more about this wood chest. I would appreciate any help you can give me. There is a stamp on one of the drawers in the shape of a triangle that reads “Made in Grand Rapids Trademark Registered.” Thank you.
— S.S., Salem, Ohio
Types of Wood on Chest Speak to Age
A The wood chest is called a “bonnet” chest because the storage space in the center with the door is
specifically designed for hats or bonnets worn by ladies and gentlemen of the period. The wood on the drawer fronts and probably the top is striped mahogany veneer. The wood in the structural pieces, the rails (the horizontal pieces between the drawers) and the stiles (the vertical pieces that make up the side supports and legs) are made of birch that has a dark aniline dye to make them resemble mahogany. This type of mixed woods and coloring process was common from the turn of the century to the 1960s.
The style of the wood chest, the shape of the mirror and the hardware indicate that it was made in the first quarter of the 20th century, sometime before World War I. If the glass in the mirror is original to the piece, it will have the date of manufacture on the reverse of the glass itself. All American plate mirror originally incorporated into furniture in the 20th century is dated. The identifying chest requires removing whatever backing is on the mirror to see the gray reverse side of the mirror. But the real clue here is the triangle stamp. Around the turn of the century, Grand Rapids manufacturers needed to protect the reputation of the city against imposters using the term “Grand Rapids” in advertising. Every piece of furniture made in Grand Rapids by members of the Furniture Manufacturers Association from 1899 to 1913 bore this red triangular mark.
The chest appears to have been refinished. The original finish would have been shellac, which probably would have darkened considerably by now. Chests like this sell in the $300 to $500 range at good auctions.
One Piece or Two Determines Process for Repairing Desk's Tambour
Q I read your column often. I have an antique roll top desk with bad webbing in the roll top. What would you use to replace it and what is the procedure for doing it? Thanks.
— J.B., Harmony, Pa.
A The roll top itself is called a tambour and the webbing used to make it flexible is usually canvas or sailcloth. Over the years the canvas gets weak and tears in the spaces between the slats of the tambour and that usually is the problem. The first step is to remove the tambour from the desk. If the tambour has a protruding handle rather than finger spaces it probably will have to be removed first. If your desk is a two piece desk, one where the top section can be released by screws, your job is much easier. Just release the top section of the desk from the base, lift it off with the tambour in place and put the whole arrangement on a table. The tambour should now just feed itself out the front of the top section. You may have to release a stop block on the bottom of the tambour. Just be careful it doesn’t free-fall to the floor.
If the desk is not a “two-piecer,” locate the exit for the tambour in the back of the desk or behind the
modesty panel between the pedestals. You may have to remove a trap door or a block of some sort, but it can be done. Then feed the tambour out the back or bottom of the desk.
Place the tambour face down on a surface large enough to spread it flat with some working room around it. Next determine if you are going to need to remove the old canvas. If the canvas is just torn or broken between the slats, there is no need to remove it. If the canvas is loose in large areas or greatly deteriorated then it must be removed entirely, which is the last resort.
Next, clamp a board or a raised straight edge to the edge of the surface to make sure the slats stay in alignment. Then use fresh contact cement to adhere new canvas directly to the old. It is not necessary to cover the entire back with new canvas. Usually three strips, six to nine inches wide, applied vertically against the direction of the slats one on each edge and one down the middle will do the job. It’s easier to handle the smaller strips than one large sheet. Be sure the tambour remains square during the entire procedure. Clamp it in sections if necessary to keep it aligned. Then just reinstall the tambour after cleaning out the channel it runs in and applying some silicone lubricant.
If you find that the old canvas should be removed, first take the time to number the slats on the back, in order, just in case something goes awry in the process. Then dissolve the old glue with warm water and vinegar and work a small section at a time. After the canvas is off use a cabinet scraper or a chisel blade to scrape the backs of the slats clean. Allow them to dry overnight and apply new canvas. If you need to remove the old canvas, clamping the tambour in place is especially important to keep it in original alignment and to keep from warping as it dries overnight.
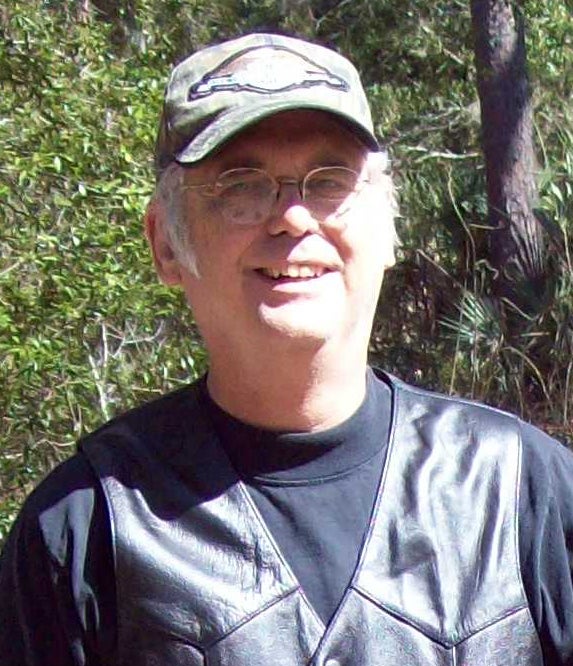
With more than 30 in the antique furniture business, Fred Taylor is a household name when it comes to the practical methods of identifying older and antique furniture: construction techniques; construction materials; and style.